RonaScreed FastDry Prompt (formerly RonaScreed 8 Day Overlay) is so-called because it is a fast-drying screed additive that enables a 50mm thickness of 3:1 sand/ cement screed to be overlaid with moisture sensitive floorings such as resilient floorings, carpet, quarry tiles, ceramic tiles and stone tiles after 4 days of air curing in good drying conditions. All references to drying of Ronacrete screeds relate to testing of screeds at 200C & 60-65% air humidity. Ronacrete Laboratory tests and independent tests by Vinci Technology confirm the predictability of results shown in the technical data. RonaScreed FastDry Prompt gains strength at a faster rate than a typical sand cement screed and strengths greater than 20N/mm2 are achievable after 24 hours at 200C, allowing early access to following trades.
RonaScreed FastDry Prompt has been used for decades where construction programs are compressed, leaving little time for a sand/ cement screed to dry and where contractors wish to reduce the incidence of damage to screed by following trades, by having screeds applied later in the construction program than would otherwise be possible. RonaScreed FastDry Prompt has been extensively used in the education sector, particularly where underfloor heating is specified, and the product was once specified as standard for screeds in schools and colleges by several county architects’ departments. The adoption of design & build contracts by some councils has led to a more fragmented approach to the specification of screeds and there was a period when calcium sulphate screeds became widely chosen by design & build contractors, they are undoubtedly cheap and large areas can be laid very quickly but there are drawbacks, particularly when construction programs are short.
Drying of standard sand/ cement screeds
BS 8204-1 “Concrete bases and cementitious levelling screeds to receive floorings — Code of practice” section 6.11.1 suggests the following calculation for drying of screeds with no fast-drying additive “with levelling screeds, one day should be allowed for each millimetre of thickness for the first 50 mm, followed by an increasing time for each millimetre above this thickness. It is therefore reasonable to expect a levelling screed 50 mm thick, drying under good conditions, to be sufficiently dry in about 2 months.” It is generally accepted that between 50mm thickness and 75mm thickness, 2 days should be allowed for drying of each millimetre of thickness and a 75mm thick screed with no additive might be expected to take 100 days to dry to 75% humidity in good drying conditions. In poor drying conditions when humidity is high and/ or temperature is low, drying may take considerably longer, especially if moisture evaporating from screed and plaster is not extracted by open windows and doors or other means.
Testing conditions
When comparing specific drying claims made by other producers, it is advisable to look at the drying conditions under which samples were tested. Ronacrete products are tested after drying at a room temperature of 200C temperature and 60-65% air humidity. Tests carried out on samples cured at higher temperature and lower air humidity will produce apparently better drying data, the specifier or contractor should consider how close the curing conditions are to the reality of site conditions.
Limiting factors
There are a number of key factors involved in how quickly flooring may be applied to a screed:
- The temperature in the room – lower temperature will increase drying time
- Humidity in the room – higher air humidity will increase drying time
- The mix design of the screed, for example RonaScreed FastDry Prompt is 3 parts sand: 1 part Portland cement by weight and will reach 75% RH after 4 days @ 50mm thickness and after 6 days @ 75-100mm thickness
- Mixing equipment, the mixer must be a forced action mixer; free fall mixers are not acceptable.
- The use of retarders – retarders added to the screed at a batching plant or in volumetric mixers will severely affect drying of the screed.
- Dryness requirements of the flooring – most flooring products require a screed surface relative humidity of ˂ 75% for application. Bonded wood floorings generally require a considerably lower moisture content and RonaScreed FastDry Prompt is not tested for the requirements of wood floorings.
- Dryness testing – the following is the only equipment recognised by Ronacrete for accurate testing of screed surface relative humidity:
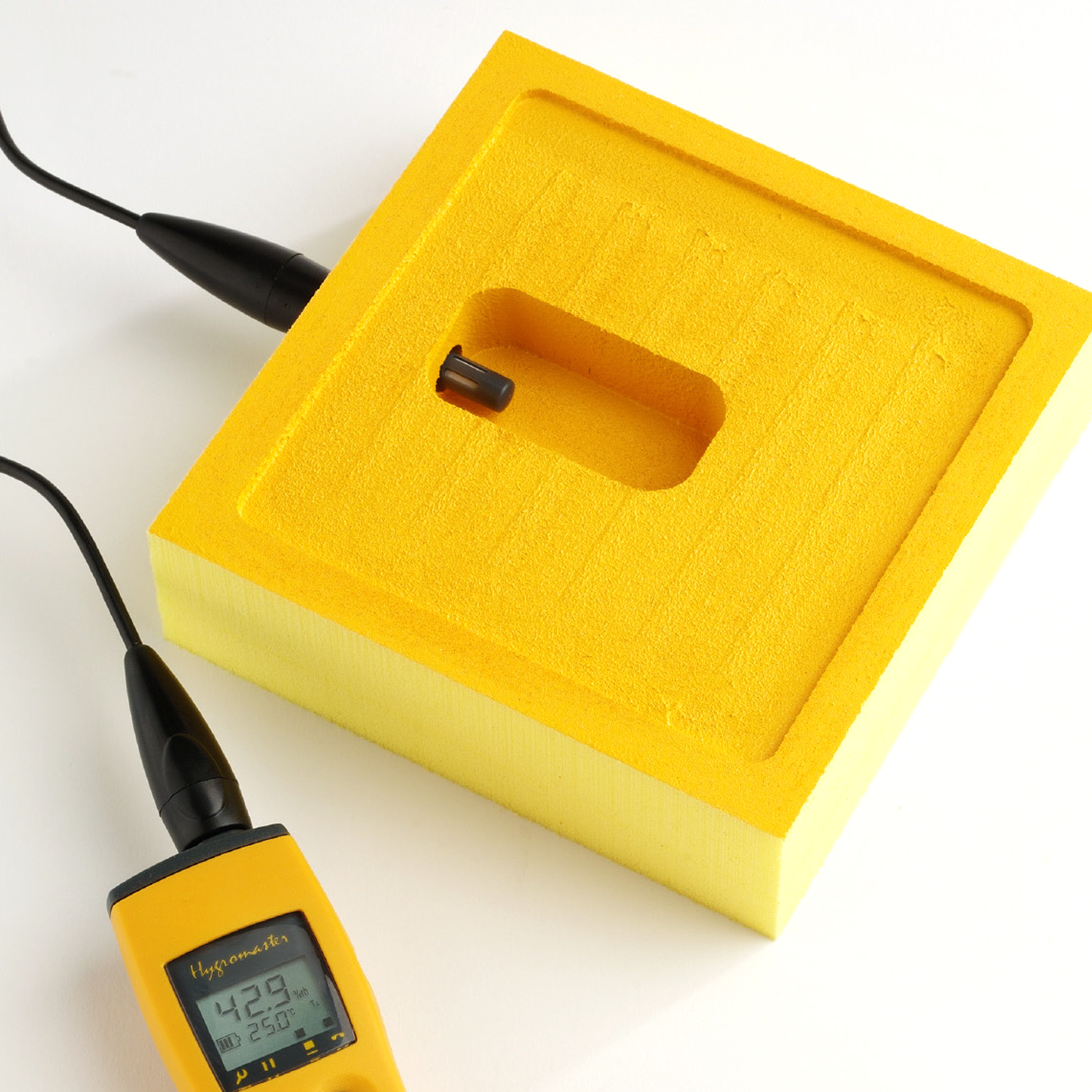
Drying of RonaScreed FastDry Prompt Mix Design 3
Drying of RonaScreed FastDry Prompt Mix Design 3 (3:1 by weight) has been tested at 50mm, 75mm and 100mmthickness. At 50mm thickness, RonaScreed FastDry Prompt Mix Design 3 dries to 75% RH after 4 days of air curing and at 75-100mm thickness, RonaScreed FastDry Prompt Mix Design 3 dries to 75% RH after 6 days of air curing. 75% relative humidity at the surface indicates that the screed is sufficiently dry for application of resilient floorings, carpet, quarry tiles, ceramic tiles and stone tiles. Ronacrete Laboratory tests and independent tests by Vinci Technology confirm the predictability of results shown in the technical data. Drying time on site will vary according to site conditions. Increased screed thickness, lower temperature and higher humidity will lengthen the drying period; increasing the aggregate/ cement ratio will also increase drying time.
Screeds should be sufficiently dry and strong before forced drying or commissioning of underfloor heating commences, RonaScreed FastDry Prompt Mix Design 3 dries to 80% RH after approximately 2 days of air curing at a thickness of 75mm and will gain a high proportion of its ultimate strength after the same period of curing. At this stage, forced drying or commissioning of underfloor heating may commence, underfloor heating may be turned on and the temperature may be gradually increased in accordance with the instructions of the heating manufacturer. Forced drying or commissioning of underfloor heating should be delayed at lower temperature and when air humidity is high or when RonaScreed FastDry Prompt has been added to a weaker mix design.